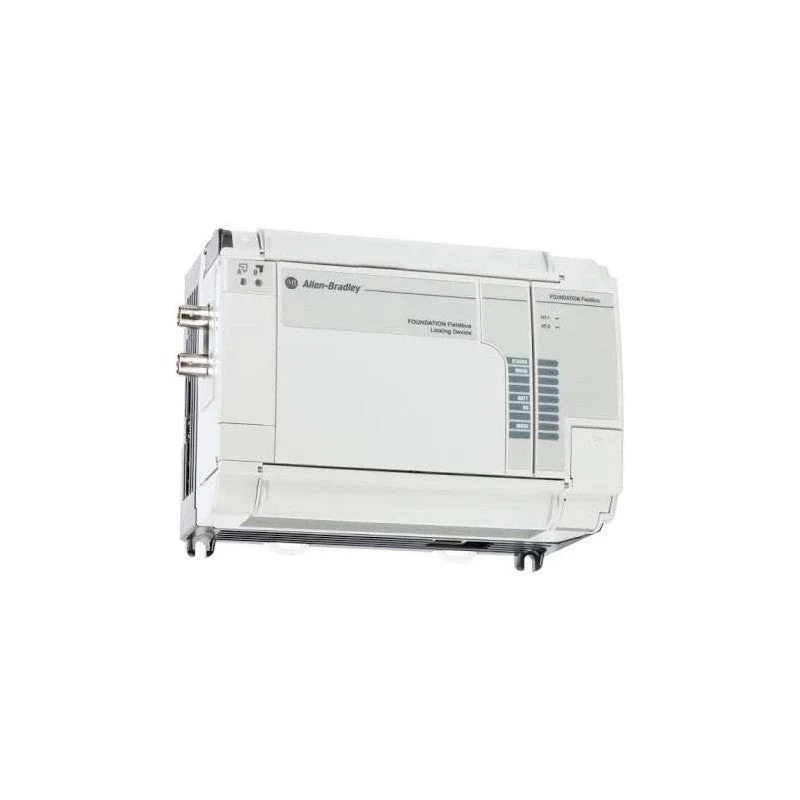
Fieldbus – What Is It?
For many years, industrial networks relied on RS232 serial communications, which limited communication to direct serial connections between devices. In such systems, if there were N devices, only N-1 devices could engage in communication simultaneously. To overcome these limitations, the Fieldbus International Standard was developed in the late 20th century, introducing a scalable and flexible communication solution for industrial automation.
What is Fieldbus?
Fieldbus is a digital, two-way communication system that connects field devices (such as sensors, actuators, and controllers) in a network. It enables input devices (like Ethernet switches and sensors) to communicate with output devices (such as valves and drives) without requiring direct, individual wiring to a central controller. This leads to simplified wiring, reduced installation costs, and enhanced process control.
Fieldbus in Complex Automated Systems
In complex automation systems, different hierarchical levels communicate through various network types. While higher levels use Ethernet for non-time-critical communication, lower-level devices rely on Fieldbus for fast and reliable interactions. Fieldbus connects PLCs with local devices like motors, sensors, and actuators, replacing traditional point-to-point wiring with a networked solution.
Fieldbus Cards
Fieldbus cards interface with control systems (e.g., pCO controllers) via serial links using standard or proprietary protocols. These cards are available in different configurations to support various communication standards, enhancing system flexibility and expandability.
Common Fieldbus Protocols
Different industries use different Fieldbus protocols based on specific needs. Popular protocols include:
-
Foundation Fieldbus
-
Profibus
-
DeviceNet
-
Modbus
Each protocol has its own specifications, compatibility considerations, and use cases. Choosing the right one depends on the application, desired performance, and system compatibility.
Design Specifications
Key design specs to evaluate include:
-
Max Connections: Number of supported devices or ports.
-
Connection Types: Supported media like coaxial, twisted pair, or fiber-optic cabling.
-
Modularity: Expandability through add-on modules like I/O cards.
Performance Specifications
Performance metrics include:
-
Accuracy: Closeness of measurements to actual values.
-
Drift: Change in accuracy over time.
Features and Capabilities
Fieldbus systems offer a range of functionalities:
-
Measurement & Calibration: Real-time monitoring and self-correction.
-
Documentation: Automated storage of process data.
-
Data Analysis: Aggregation and interpretation of field data.
-
PID Control: Local execution of control loops.
How Fieldbus Works
Fieldbus allows multiple devices to communicate over a single network, eliminating the need for individual point-to-point wiring. Time-multiplexed messages are transmitted in short, encoded packets, providing efficient data transfer with reduced wiring.
Fieldbus Network Layers
-
Sensor Bus Network: Connects simple devices like switches and sensors.
-
Device Bus Network: Includes complex devices like VSDs and MCCs.
-
Control Bus Network: Utilizes PLCs for centralized control.
-
Enterprise Bus Network: Connects the entire enterprise for data analysis and coordination.
Network Topologies
-
Ring: Devices connect in a closed loop.
-
Line (Bus/Daisy Chain): Sequential connection.
-
Star: Central hub connects to each node.
-
Tree: Hierarchical branching of nodes.
Benefits of Fieldbus
-
Reduced Cabling: Fewer wires mean easier installations.
-
Lower Costs: Faster installation and less hardware.
-
Higher Reliability: Short signal paths reduce error rates.
-
Interoperability: Devices from different manufacturers work together.
-
Flexibility: Easy integration of additional functions or devices.
Advantages for End Users
-
Control-in-the-field
-
Closed-loop sensor feedback
-
Fewer devices and hardware
-
Faster commissioning
-
Advanced diagnostics
Function Blocks in Fieldbus
Function blocks perform specific control or diagnostic tasks. These include:
-
Standardized and vendor-specific blocks
-
Resource blocks for device ID and performance
-
Transducer blocks for sensor/actuator parameters
Device Description Language (DDL)
DDL enhances the ability to describe device parameters, units, limits, and more. This allows manufacturers to customize devices without sacrificing compatibility.
Distributed Control in Fieldbus
Unlike traditional DCS systems that centralize control, Fieldbus distributes intelligence among devices. Control blocks handle operations like PID control at the device level, reducing the burden on central controllers.
Message Types
-
Cyclic: Regular process data messages
-
Acyclic: On-demand messages for diagnostics or configuration
New Installations vs Upgrades
Fieldbus is ideal for new installations due to reduced cabling and hardware needs. It can be integrated into existing DCSs for upgrades, although partial replacements may be necessary. Upgrading allows continued use of some legacy infrastructure while enhancing capabilities.
Final Thoughts
Fieldbus technology has revolutionized industrial automation by enabling efficient, scalable, and reliable communication between field devices and control systems. Its flexible design, reduced wiring needs, distributed control architecture, and diagnostic capabilities make it a preferred choice for modern automated environments. Whether implementing a new system or upgrading an existing one, Fieldbus provides a robust foundation for intelligent and connected industrial operations.
Contact PLG Automation today:
Email: sales@plgautomation.com
Phone: 800-906-9271